EVC2: Hydrotreatment to HVO
The HVO feedstocks are the same as for FAME biodiesel, and the pre-treatment is in principle the same, with the exception that the HVO process can process FFA together with the triglycerides. HVO type of biofuels can be produced in stand-alone facilities, in converted existing oil refineries, or co-processed in existing oil refineries.
The first stage, the so-called hydrotreatment, takes place at 3 - 5 MPa (5 - 15 MPa for co-processing in fossil hydrotreater) pressure and at temperatures between 300 °C and 450 °C, over a catalyst in a trickle column reactor, to which hydrogen is added with the liquid feed. The hydrogen is today mainly derived from fossil sources[1], but in the future it could be derived from the bio-LPG produced in the process or from RE power.
Initially, hydrogen saturates any double bonds of the triglycerides followed by a cleavage to fatty acids and the hydrogenation (hydrogen removes the acid group oxygen as H2O) of glycerol to propane (i.e. bio-LPG) and water. Finally, the fatty acids undergo a combination of hydrogenation or decarboxylation (the acid group oxygen leaves as CO2), the reaction split depends on the catalyst and operating conditions used. This results in straight chain alkane hydrocarbons.
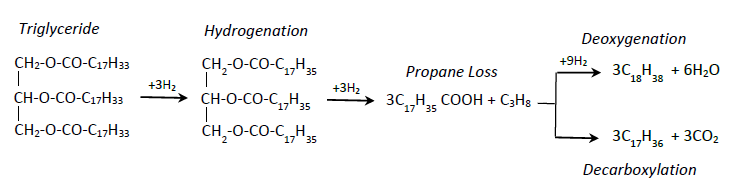
The second stage of hydroprocessing involves the catalytic isomerisation and cracking of the straight chain alkanes, at 300 - 400 °C, the severity of which is dictated by the desired fuel products. The result of this step is a mixture of straight chain, branched chain, and cyclic paraffinic hydrocarbons at similar or lower average carbon number than the original straight chains. The change in the molecular structure of the hydrocarbons allows aligning the properties to the specification of marketed fuels for the local climatic conditions. The various desired hydrocarbons product fractions, e.g. HVO diesel and/or HEFA kerosene, gasoline and naphtha fractions are then separated by distillation.
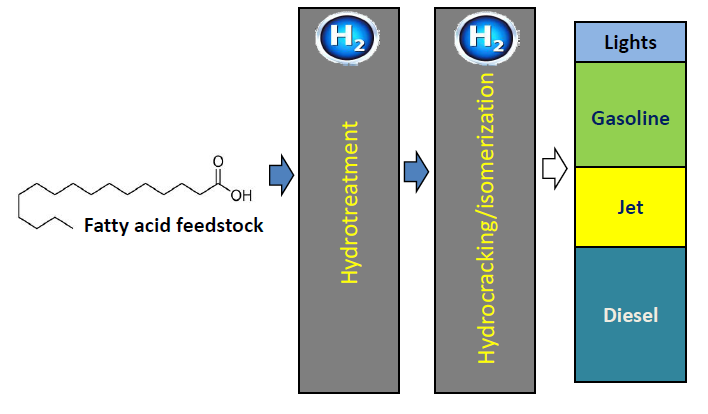
Simplified process scheme for the two stages of hydroprocessing
In the EU, if the GHG reduction threshold are achieved, HVO diesel can be considered as a biofuel or an advanced biofuel, eligible for double counting, depending on the feedstock used. Both categories can be produced in the same plant, if capable of using waste and residues materials.
Global production in 2017 was 6.5 billion liters (65 TWh or 5.6 Mtoe). There are some over 25 plants worldwide3, including co-processing. The EU has 14 plants, including co-processing facilities, that in 2018 had 2 million liters production and 5 million liters capacity (some plants were being commissioned in 2018, and all co-processing capacity not being fully used). There are at least three dedicated plants in the USA and China and one plant in Singapore. Neste is the biggest producer with three plants located in Helsinki, Rotterdam and Singapore. The facilities are continuously being upgraded, to improve in production capacity and make better use of by-products.
Global production will be limited by the limited amount of sufficiently cheap feedstock available.
Fact Sheet: Hydrogenated vegetable oil (HVO)
Acknowledgement: Large parts of the texts were taken from Lars Waldheim´s contribution to the report “The Contribution of Advanced Renewable Transport Fuels to Transport Decarbonisation in 2030 and beyond”
[1] mainly produced via steam reforming of natural gas or refinery fuel gas