FT-Liquids & Biomass to Liquids (BtL)
Introduction
The term Biomass to Liquid BtL is applied to synthetic fuels made from biomass through a thermochemical route. The objective is to produce fuel components that are similar to those of current fossil-derived petrol (gasoline) and diesel fuels and hence can be used in existing fuel distribution systems and with standard engines. They are also known as synfuels.
Biomass is pretreated and then converted to synthesis gas via gastification. The resulting syngas is then cleaned prior to conversion to liquid biofuels, typically via Fischer Tropsch or the Mobil Process outlined below.
Although the individual steps for production of BtL are well known (and have been demonstrated successfully at industrial scale), integrating the various technologies for commercial production of BtL has proved challenging. In recent months some promising industrial scale demonstration projects have been cancelled due to uncertainty surrounding the regulatory environment for advanced biofuels in Europe. However, R&D&D on Biomass-to-Liquid continues, as outlined below.
Note: Some European demonstration projects on gasification have been discontinued in recent months for various reasons, however summary information on the 'project history' and technology developed is retained on this page for reference purposes.
- Download the EBTP
Value Chain Fact Sheet #1 Biomass to Liquids (180 Kb)
BtL demonstration projects in Europe
BA GreenSky project shelved, citing lack of government support
On 6 January 2016, British Airways announced that it has been forced to shelve its GreenSky project to create 16m gallons of jet fuel from waste every year, partly due to a lack of government support [Source: The Guardian, UK]. British Airways planned to use 600,000 tonnes of MSW (collected in London) to produce over 50000 tonnes of biojet fuel and 50000 tonnes of biodiesel annually. The GreenSky project was to have used Solena's Plasma Gasification (SPG) technology, which can process 20-50% more waste than conventional gasification technologies, and Velocys technology for production of the jet fuel.
The BioTfuel BtL demonstration project
BioTfueL is a joint project launched by five French partners and Uhde. BioTfueL aims to integrate all the stages of the BTL process chain and bring them to market. This involves the drying and crushing of the biomass, torrefaction, gasification, purification of the synthesis gas and its ultimate conversion to second generation biofuels using Fischer-Tropsch synthesis.
The project will use Uhde's proprietary PRENFLOTM™ gasification process with direct quench (PDQ). The procees can utilise a wide range of feedstocks, allows high energy efficiency and enables very pure synthesis gas to be produced.
The overall budget for the BioTfueL project is 112.7 million euro. The project includes the construction and operation of two pilot plants in France to produce biodiesel and biokerosene based on biomass gasification.The plants are scheduled to go into operation in 2012 [Source: Uhde GmbH].
Bioliq Pilot Plant at Karlsrhue
The bioliq® pilot plant at Karlsruhe Institute of Technology (KIT) is running successfully along the complete process chain. All stages of the process have now been interconnected: Flash pyrolysis, high-pressure entrained flow gasification, hot gas cleaning, and synthesis. In March 2015, Air Liquide announced it has provided key technologies for the pyrolysis of biomass and gas synthesis as well as the oxygen supply needed for the gasification process.
CEA / Air Liquide - SYNDIÈSE-BtS project, Bure-Saudron
Air Liquide and CEA, France, are developing an innovative process for converting biomass into synthesis gas - the SYNDIÈSE-BtS project, Bure-Saudron. CEA is developing a novel mechanical pretreatment processes for biomass, which will reduce energy consumption compared to thermochemical pretreatments. Air Liquide is developing techniques to convert the pretreated biomass to syngas in an oxy-burner at 1300-1400° C. In May 2013, the began development of a pilot plant to test the concept at 1 tonne per hour.
In 2009, CEA announced a BtL pilot plant in Bure Saudron using 75000 tonnes of foresty and agricultural residues to produce ~23000 tonnes/year of biofuel (diesel, kerosene and naptha). This project added hydrogen during the synthesis stage to optimise the ratio with carbon monoxide [Source CEA].
Fulcrum Bioenergy - Sierra Biofuels MSW to Jet Fuel and Diesel facility
In May 2105, Fulcrum Bioenergy Inc., announced it has awarded a $200m engineering, procurement and construction (EPC) contract to Abengoa for the construction of the 10 MMgy Sierra BioFuels facility to convert MSW into syngas, followed by a Fischer Tropsch step to create second generation biodiesel and bio jet fuel.
In September 2014, Fulcrum Bioenergy announced a $105m 'Biorefinery Assistance Program' loan guarantee from the USDA, as well as a $70 million grant under the US DoD Defense Protection Act, which will support development.
Fulcrum has entered into a long-term, zero-cost MSW feedstock agreements with Waste Management and Waste Connections, two of the largest waste service companies in North America, and a fuel off-take agreement with Tenaska BioFuels. The Sierra BioFuels Plant is expected to be one of the United States’ first fully operational, commercial-scale MSW-to-renewable fuels production plants.
In Summer 2014, Cathay Pacific Airways announced that it is investing in Fulcrum Bioenergy Inc., the parent company of Fulcrum Sierra BioFuels, LLC, and has negotiated a long-term supply agreement with Fulcrum for 375 million gallons of sustainable aviation fuel over 10 years. This would represent about 2 % of the airline's annual fuel consumption. [Source: Fulcrum Bioenergy website & USDA Press Release].
Cool Planet 'Reformate' commercial facility, Louisiana, US
Cool Planet (with investors including BP, Google Ventures, ConocoPhillips and GE), is using a thermo-mechanical fractionation system (pyrolyzer) to convert wood waste and energy crops into hydrocarbon chains (gases). These are converted via catalysts to high-octane, renewable gasoline blendstocks (known as "Reformate"), which can be used to enhance the energy content of gasoline, diesel, and jet fuel. Pine chips will be the feedstock source for the Cool Planet facility, but the process can use almost any type of renewable cellulosic material. BioChar is produced as a by-product for soil enhancement and carbon sequestration [Source: Cool Planet].
In February 2014, Cool Planet Energy Systems broke ground on a commercial facility 'Project Genesis' in Alexandria to produce 10m gallons per years of renewable gasoline. In October 2014, it was announced USDA has reached an agreement with Silicon Valley Bank to provide a $91 million Biorefinery Assistance Program (Biorefinery, Renewable Chemical, and Biobased Product Manufacturing Assistance Program, 2016) loan guarantee to Cool Planet to help the company finish construction of the plant. A $168m investment for three production facilities in Louisiana was originally announced by Cool Planet in September 2013.
Velocys / Red Rock Biofuels
In July 2015, Red Rock announced an ageement to supply FedEx Express with 3m gallons p.a. of bio jet fuel from 2017. Red Rock also has agreements to supply Soutthwest Airlines. In October 2014, it was announced that Red Rock Biofuels had been awarded a $70m USDD biofuels contract to use woody biomass to produce 12m gallons of advanced biofuels using Velocys Fischer-Tropsch technology.
UPM Stracel BTL
A final decision on whether or not the UPM Stracel BtL facility will proceed is reportedly pending, due to ongoing uncertainty over the regulatory environment for advanced biofuels in Europe.
On 18 December 2012 it was announced that the UPM Stracel BTL project, France, had been selected to receive counterpart funding of €170m under the first call for proposals of the NER300 funding programme for innovative low-carbon technologies. The Project concerns the construction and operation of a second generation Biomass-to-Liquid (BtL) plant on the Strasbourg site of the UPM Group, which already owns and operates a paper mill on the same site (Stracel). The Project is based on a prototype developed in cooperation with the technology provider using a gasification process. The Project is based on the application of novel pressurized oxygen blown biomass gasification technology. The BtL plant will be integrated into the paper & pulp production line, enabling exchanges of energy and products. The plant will use about 1 million tonnes of woody biomass and will have an annual output of 105 000 tons of biofuel. Using mainly wood feedstock, the Project aims to produce and sell biodiesel (80%) and bionaphtha (20%). The proposed technical solution is based on the following main components: feedstock handling, gasification, raw gas cleaning, gas-to-liquid conversion, liquid treatment and storage, and power generation.
Discontinued BtL Projects
Ajos BTL
In February 2014, The Board of Directors of Vapo Oy made the decision to freeze project planning for the biodiesel plant planned for Ajos in Kemi. According to the companys's press release: The final, decisive blow to the project was that the EU’s climate and energy strategy published in January did not agree on new binding limits for the share of the renewable component in traffic fuels after 2020. “In this situation it is not possible to conclude long-term commitments, which would have created the financial preconditions for Vapo’s biodiesel project.”
It was also announced that the AJos BtL project, Finland, has been selected to receive counterpart funding of €88.5m under the first call for proposals of the NER300 funding programme for innovative low-carbon technologies.The Project concerns the design, construction and operation of a biofuel-to-liquid (BtL) plant in northern Finland, with a gasification capacity of 320 MW and an annual output of 115000 t/y of biofuel using close to 950000 t/y of woody feedstock and 31000 t/y of tall oil. The technical solution is based on the following main components: biomass pre-treatment, gasification island (comprising two gasification lines of 160 MW each and an air separation unit), gas cleaning and compression, gas-to-liquid conversion (Fischer-Tropsch) including refining, processing and storage of products. The Project will produce and sell biodiesel and bionaphta in the Baltic Sea area, with a focus on Finland and Sweden. Principal off-takers are expected to be diesel and petrol retailers.
[Source: SWD(2012) 224 final: NER300 - Moving towards a low carbon economy and boosting innovation, growth and employment across the EU]The preparation work in the project had been carried out by the Forest BtL Project established by Metsäliitto and Vapo.
Linde Engineering Dresden GmbH had signed an agreement with Forest BtL Oy, Finland for licensing of Carbo-V® biomass gasification technology (see also Choren archive information below). Carbo-V technology was operated for short term, could not be put into stable operation but the operation of ~ 1200-2000 hrs. has shown the process principle (source: Linde presentation during IEA Workshop 2014).
NSE Biofuels BtL Demonstration Plant
NSE Biofuels Oy - a joint venture between Neste Oil and Stora Enso operated a BtL demonstration plant at Stora Enso’s Varkaus Mill in Finland in 2010. The output was 656 t/a from a 12 MW gasifier. As well as providing test data and operating experience, the plant also reduced greenhouse gas emissions as wood-based gas from the plant replaced oil in the pulp mill’s lime kiln, making the Varkaus integrate virtually fossil fuel free. NSE Biofuels (in partnership with Foster Wheeler and VTT) planned to develop a commercial production plant at one of Stora Enso’s mills with a projected output capacity of 100000 t/a and a potential launch date of 2016.
However, in August 2012 Neste Oil and Stora Enso announced that they had decided not to progress with their plans to build a biodiesel plant, for which the two companies had applied for funding under the EC's NER 300 programme. Although the technology has worked well at the demonstration plant (above), the project was not among those listed [in the NER300 intermin report] as scheduled to receive funding. Even with public funding, significant investment would also have been required for the commercial plant. [Source: Neste Oil website].
© Copyright Stora Enso
The NSE Biofuels BtL demonstration plant.
Choren gasification technology sold to Linde
Previously, the world's first commercial BtL Plant was under construction in Frieberg Saxony, utilising the Choren Carbo-V ® Process. Choren Industries filed for insolvency in July 2011. A new investor for Choren Components was announced in October 2011. On 9 February 2012 Choren's biomass gasification technology was sold to Linde Engineering Dresden, who will further develop the Choren Carbo-V® technology used to produce syngas.
The Choren Carbo-V ® Process
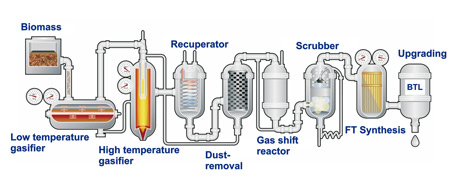
© Copyright Choren
The Choren Carbo-V ® Process View at larger size>>
The Carbo-V® Process is a three-stage gasification process resulting in the production of syngas:
- low temperature gasification,
- high temperature gasification and
- endothermic entrained bed gasification.
The Fischer-Tropsch (FT) process is then used to convert the synthesis gas into an automotive fuel SunDiesel®.
The Choren plant used the proprietary Shell Middle Distillate Synthesis (SMDS) technology. Syngas production is followed by a modified version of the Fischer-Tropsch process. This favours the production of long chain waxy molecules, which are unsuitable for transport fuels, but substantially reduces the amounts of unwanted smaller hydrocarbons or gaseous byproducts. The hydrocarbon synthesis step is followed by a combined hydro-isomerisation and hydrocracking step to produce the desired, lighter products [Source: Shell Middle Distillate Synthesis: Fischer Tropsch catalysis in Natural Gas Conversion to High Quality Products, J. Ansorge, Shell International Oil Products B.V.].
The SMDS process has been implemented on a commercial scale at the $18 billion fossil gas-to-liquids (GTL) plant, developed by Qatar Petroleum and Shell, with a capacity of 260,000 barrels oil equivalent a day.
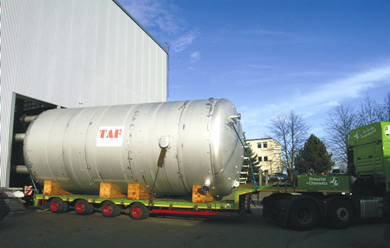
© Copyright Choren
Reactor being delivered to the Choren BTL plant.
View at larger size>>
The Choren website listed a number of advantages for SunDiesel®:
- High cetane number and therefore much better ignition performance than conventional diesel fuel,
- No aromatics or sulfur and significantly reduces pollutants from exhaust emissions,
- Can be used without any adjustment to existing infrastructure or engine systems,
- Largely CO2-neutral.
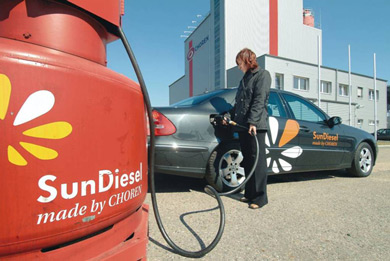
© Copyright Choren
SunDiesel® demonstration fuel station at Choren BtL plant
View at larger size>>
Presentation on Choren BtL plant from EBTP SPM2
European Research on BtL, thermochemical conversion and 'sustainable biodiesel'
In Summer 2013, VTT TRC Finland published a 126pp study Liquid transportation fuels via large-scale fluidised-bed gasification of lignocellulosic biomass. 20 individual BTL plant designs were evaluated based on their technical and economic performance.
In February 2013, a presentation on Status update of selected demonstration plants (thermochemical value chains) was made at EBTP SPM5.
BRISK is a €10.84M four-year initiative with €8.98M funded under EC FP7 (Ref: 284498). BRISK aims to develop a European Research Infrastructure for Thermochemical Biomass Conversion, supporting R&D on innovative processes to convert sustainable feedstocks (agricultural/forestry wastes and energy crops) into liquid, gaseous or solid fuels.
The €3.73m DIBANET project is being co-ordinated by Carbolea at the University of Limerick and is a response to the Energy 2008 Call - "Significant enhancement of the cooperation between key researchers & industries from the EU & Latin America in the field of biofuels". DIBANET stands for the "Development of Integrated Biomass Approaches NETwork" & the title of the Project is "The Production of Sustainable Diesel Miscible Biofuels from the Residues & Wastes of Europe & Latin America". There are 13 partners in the group, 6 from the EU & 7 from Latin America (LA). The total budget for the project is €3.7m. DIBANET will develop technologies to help towards eliminating the need for fossil diesel imports in the EU & LA by advancing the art in the production of ethyl-levulinate from organic wastes and residues. Ethyl levulinate (EL) is a novel diesel miscible biofuel (DMB) produced by esterifying ethanol with levulinic acid.
The Cutec institute Cutec operates a pilot plant to investigate the thermochemical conversion of different types of biomass to synthesis gas and the separation of elements of the biomass step-by-step via a hot gas filter, water-based scrubber, sulferox scrubber, etc.
Greasoline® technology converts oily and fatty raw and waste materials to hydrocarbon mixtures consisting of chemical substances occurring in fossil gasoline, kerosene and diesel fuels. These products may be used as fuels and fuel components but also as chemical raw materials. The procedure was developed at the Fraunhofer Institute for Environmental, Safety and Energy Technology UMSICHT in Oberhausen, Germany. The GREASOLINE project was supported under FP6. In contrast to biodiesel, the product is chemically identical with fossil fuels. [Source: Fraunhofer Instiute].
In 2009, a demonstration facility - The Dutch Biorefinery Initiative (DBI) - was initiated in the Port of Rotterdam by WUR and ECN with support from the Netherlands government. This included a 10 MWth entrained-flow gasification based syngas production platform for heat and power, base chemicals and BtL. Information on this project was included in the IEA Bioenergy Task 42 publication on Biorefineries.
US and Canadian research and demonstration on thermochemical conversion
In the US, Primus Green Energy has started construction of a $7m demonstration plant to produce drop-in fuels using proprietary technology based on an enhanced version of the Mobil Process. Gasification is followed by Carbon dioxide separation and scrubbing of the syngas, before a four-stage catalytic system to produce the drop-in biofuel.
In April 2013 Frontline Bioenergy received $4.2m in DOE funding for a pilot facility integrating a gasification unit, novel conditioning processes and FT to produce military biofuels.
Haldor Topsoe and Andritz Carbona, along with GTI/Uhde (Morphysorb capture of acid gases) and Phillips 66 (engine testing) have developed a 20 bbl/day wood to gasoline demonstration plant at Des Plaines, Illinois, integrating all the steps from woody biomass to gasoline production in a single facility. The project uses Topsoe Integrated Gasoline Synthesis (TIGAS), using wood pellets supplied by UPM-Kymmene. Andritz provides the gasification technology. The project has been supported by the U.S. Department of Energy (DOE), Golden Field Office, under its Integrated Biorefinery Platform program [Source: Haldor Topsøe A/S June 2013].
CRI Catalysts is the exclusive worldwide licensor of IH2 Technology, which was developed at the Gas Technology Institute (GTI ) in Des Plaines, IL. This technology directly converts virtually any biomass to high quality (ligno)cellulosic hydrocarbon gasoline, diesel or jet fuels and/or blend stocks via a two stage thermochemical process. The IH2 process technology uses specially tailored CRI catalysts in both the Hydropyrolysis and Hydroconversion stages.
Purdue University has developed H2Bioil technology, whereby biomass is rapidly heated in the presence of pressurised hydrogen. Catalysts are then used to convert the gas to "biogasoline" molecules.
Syntroleum developed Fischer-Tropsch and Bio-Synfining® technologies to convert fats, biomass, natural gas, coal, and other carbon bearing feedstocks into liquid fuels. Syntroleum has a worldwide license under ExxonMobil’s GTL patents to produce and sell fuels from natural gas or other carbonaceous substances such as coal. The company also had a joint venture Dynamic Fuels LLC (now Renewable Energy Group, Inc.) to convert animal processing wastes to biofuels.
In the United States, Maverick Synfuels has developed a modular system to produce methanol from syngas and then convert it to olefins, and in turn biofuels or other bioproducts.
Biomass to Liquid - the basics
BtL fuels may be produced from almost any type of low-moisture biomass, residues or organic wastes such as short rotation trees, perennial grasses, straw, forest thinnings, bark from paper-pulp production, bagasse, waste paper or reclaimed wood or fibre based-composites.
It is estimated that over 4m3 of BtL-fuels can be produced per hectare of land per annum. Hence, in future if 4-6 million hectares of land were used to grow energy crops, one could replace 20-25 % of the liquid transport fuel currently used.
The advantage of the BtL route to liquid transport fuels lies in the ability to use almost any type of biomass, with little pre-treatment other than moisture control. This is because the feedstock is gasified in the first stage of the process. The gas produced is then treated further to clean it, remove tars, particulates and gaseous contaminants, and to adjust the ratio of the required gases (hydrogen and carbon monoxide) to that required. The result is a balanced syngas that can be used in the second, catalytic, stage. Syngas may also be obtained by pyrolysis to form charcoal. The hot charcoal is then reacted with steam to produce watergas.
The two main catalytic processes for BtL production are Fisher-Tropsch and the Mobil Process.
Fisher-Tropsch
The Fischer-Tropsch process is a catalyzed chemical reaction in which carbon monoxide and hydrogen are converted into liquid hydrocarbons of various forms. Generally the catalysts used, for the following reaction, are based on iron and cobalt.
(2n+1)H2 + n(CO) -> CnH2n+2 + nH2O
The FT process is an established technology and is already applied on a large scale from coal or natural gas. Developed in the 1920s in Germany, it was used by both Germany and Japan during World War II and later by South Africa and to a lesser extent in the United States.
One problem is the high capital cost of the multistage process. This may be greater when biomass is used as feedstock, since the scale of operation may be limited by the distance over which biomass can be transported to the factory at an economic price. Hence, the economy of scale is decreased compared to a large coal or gas-based operation. Running and maintenance costs are also comparatively high.
Mobil Process
This is a two stage catalytic process. In the first stage LINK methanol is produced. The methanol is then used as feedstock to generate hydrocarbons of varying chain length, using a zeolite catalyst. In the conversion, a number of reactions take place in the gas phase. The conversion is initiated by the removal of water to produce dimethyl ether:
2CH3OH(g) -> CH3OCH3(g) + H2O(g)
This is followed by various other reactions in which further molecules of water are removed resulting in gradual increase in chain length.
These reactions include the following.
2CH3OCH3(g) + 2CH3OH(g) -> C6H12(g) + 4H2O(g)
3CH3OCH3(g) -> C6H12(g) + 3H2O(g)
As a result of other dehydration reactions occuring in parallel a mixture of hydrocarons is produced of which about 80% is suitable for petrol production. The mixture contains (w/w) around 50% highly branched alkanes, 12% highly branched alkenes, 7% cycloalkanes and 30% aromatics. This process has been commercialised by Methanex in New Zealand using methanol produced from natural gas.